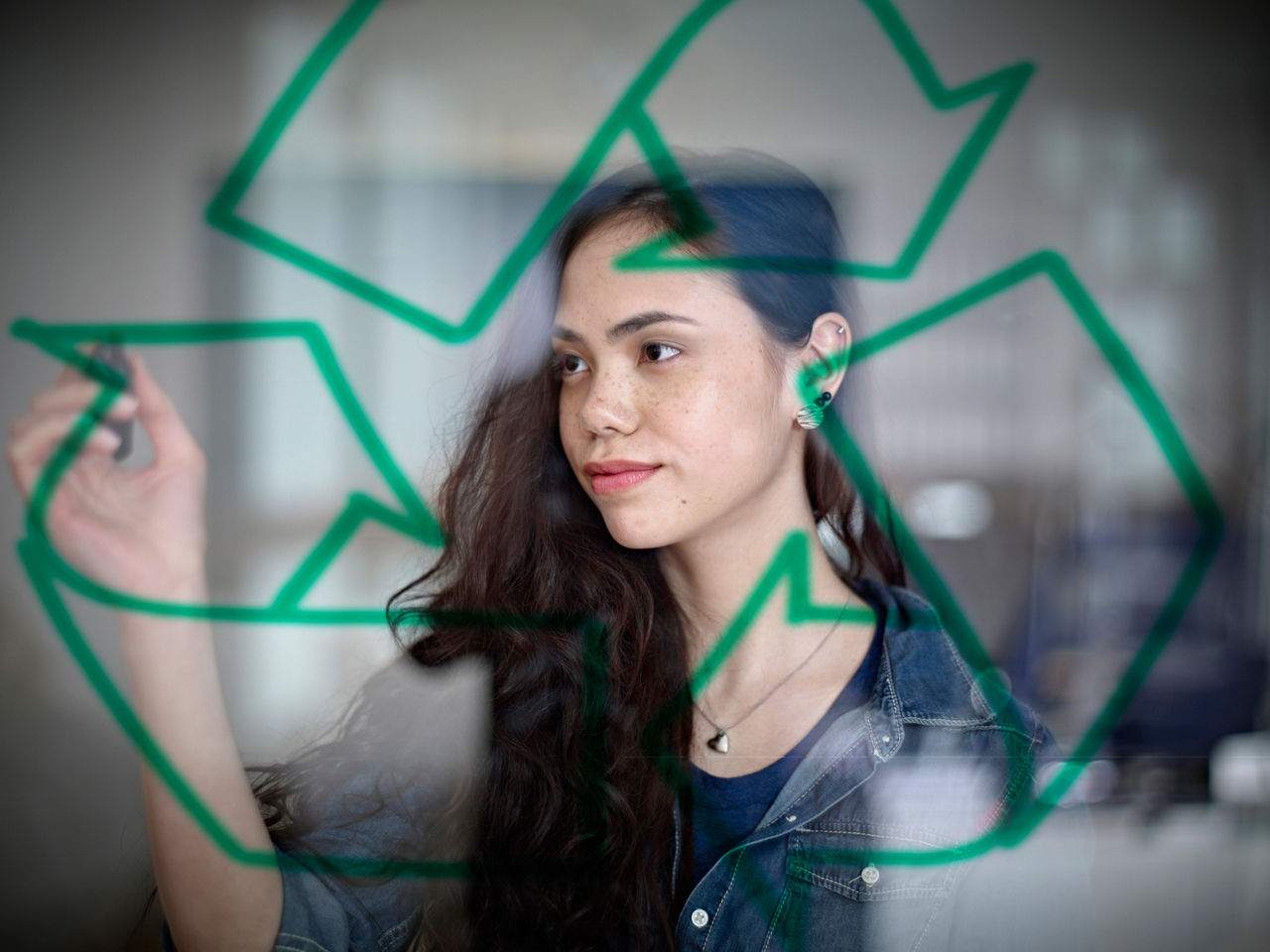
Circular Economy
The earth’s resources are finite, so it’s essential to use them efficiently. This is why Audi wants material cycles to become an integral part of the automotive value chain.
Close loops for more sustainability
Each of our vehicles contains a wide variety of valuable materials – particularly metals such as steel and aluminum, plastics and electronics parts as well as glass. In our electric models, the list also includes various materials from the high-voltage batteries.
The following applies to these raw materials and parts: After their first use in the car, it should ideally be possible to reuse them, or dismantle them without any loss of quality into their individual parts and raw materials so that they can be used again in our parts.
Audi’s vision is to return all raw materials used to the production process beyond the life cycle of the vehicles – wherever technically possible, and economically and ecologically feasible. To this end, Audi follows a holistic approach: Reduce, Reuse and Recycle. Over the long term, this principle should lead to a steady reduction in the share of used primary materials and to closing material cycles.
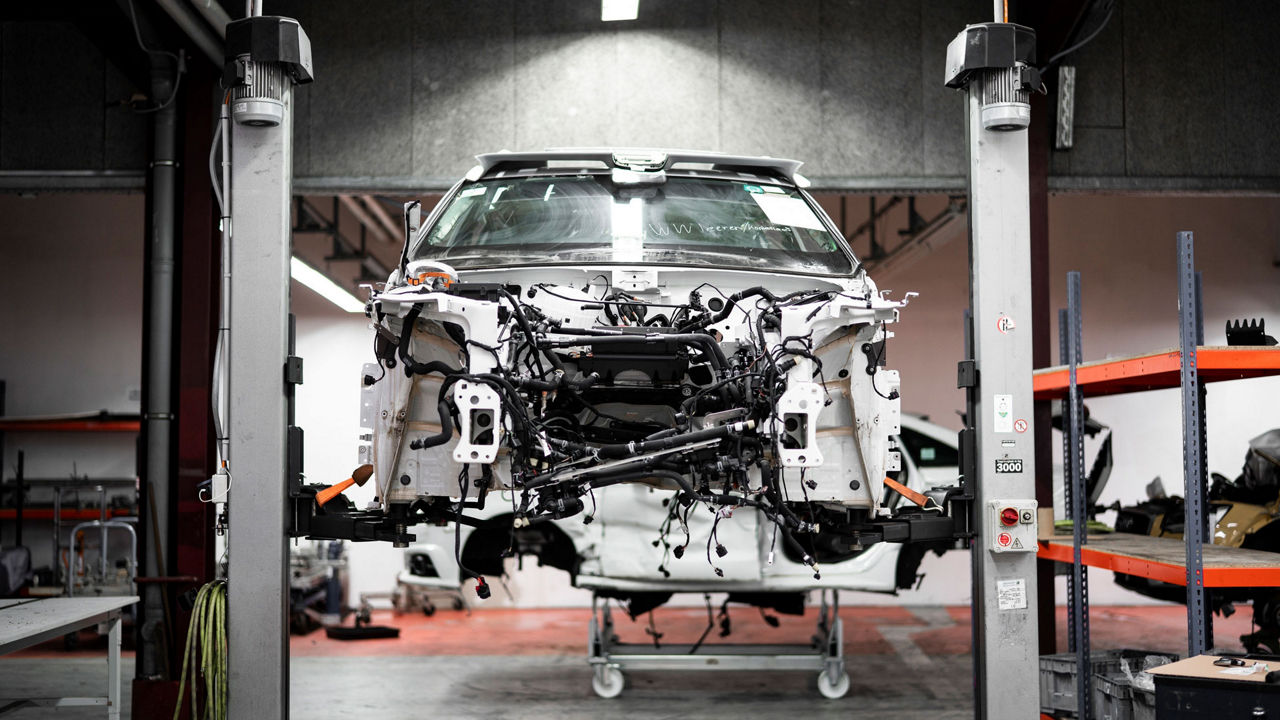
Reduce
Audi’s aim is to use all materials and resources efficiently and effectively, using only what is absolutely necessary to produce its goods. No part of the company is excluded when it comes to reduction wherever possible: from the paperless office to vehicle production free of wastewater and packaging in logistics that is as eco-friendly as possible.
More details
The starting point for measures that come under “Reduce” is often the life cycle assessment that Audi prepares for its models. Each of a car’s average of 5,000 parts is analyzed for energy consumption and emissions with the help of special software – right down to the smallest screw. This takes all steps along the value chain for each part into consideration, for example, from the mining of the aluminum ore bauxite through to processing in the press shop. Based on this assessment, CO₂ reduction measures and areas of potential optimization can be identified and evaluated along the entire manufacturing process.
One example of applying this principle is the “Aluminum Closed Loop” established at Audi at several sites. It involves making the most efficient use of aluminum as possible, since its production is especially energy-intensive. The offcuts produced in the press shops at Audi production sites are sorted by grade and returned to our suppliers. They can use the high-grade secondary material to produce new aluminum sheets (Reuse principle) and thus require less primary aluminum. This reduces the environmental impact: Using secondary aluminum enables energy savings of up to 95 percent compared with primary aluminum.
The Reduce principle also applies for the company with regard to the durability and quality of its vehicles. The longer the service life of the cars produced, the more it is in line with the Reduce principle.
Reuse
Reuse is the second approach in the circular economy. It includes, for example, the industrial processing of used parts to return them to genuine part quality. This remanufacturing provides significant added value, both ecologically and economically, since it saves costs.
More details
How Reuse works in practice can be seen in the project “Exchange 2.0,” a sustainable remanufacturing method for mechatronic parts and transmissions. Thanks to new processes, up to 80 percent of the original parts can be retained – and at a premium level. The remanufactured transmissions, for example, meet the quality criteria for new parts.
The Reuse principle was also applied within the circular economy pilot project “MaterialLoop,” which Audi used to test a highly efficient circular economy concept for end-of-life vehicles. Used parts that were suitable for reselling were removed from more than 100 vehicles dismantled for the project in order to be installed in other vehicles in the course of repair work.
Reuse or recycle? With the growing number of scrapped high-voltage batteries from electric cars, this is a question the automotive industry is addressing. For that reason, Audi has developed an analysis tool that provides an answer: The BattMAN ReLife software checks the state of health of high-voltage batteries. Depending on the capacity detected by the inspection system, the high-voltage battery can in future be reinstalled in a vehicle in whole or in part, be given a second life as a mobile or stationary energy storage system, or valuable materials like zinc or aluminum can be recycled.
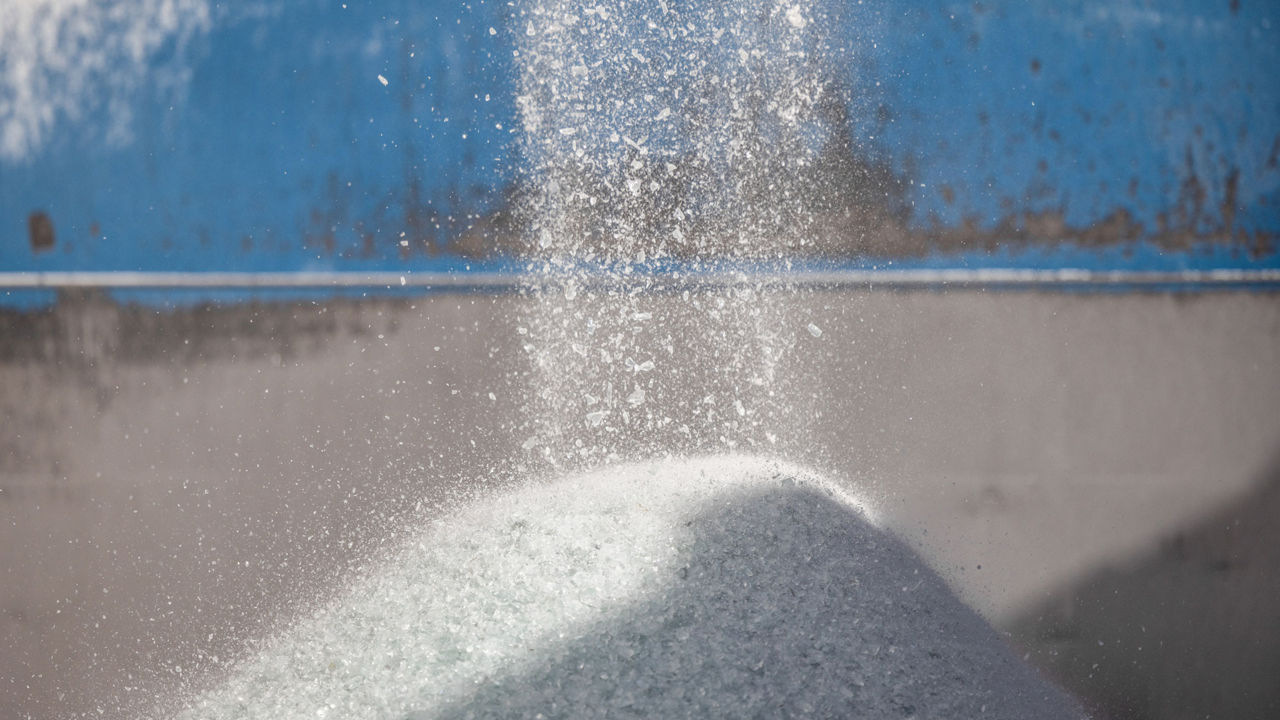
Recycle
When it comes to recycling, it’s the finer points that matter to Audi. First, because there are legal requirements* involved in this topic. And, second, because recycling can mean both reuse and remanufacturing.
Since Audi’s aim is to have a circular economy in the narrower sense with as many recycled materials as possible, the company is endeavoring to avoid what is referred to as downcycling. In practice that means returning the material to an automotive cycle ideally without any loss of quality.
More details
The focus at Audi in this regard is currently on the four largest material groups that make up today’s end-of-life vehicles: glass, plastic, steel, and aluminum. In the MaterialLoop project, involving 100 end-of-life vehicles, Audi tested how as many material cycles as possible could be closed on balance.
Regarding the subject of glass, Audi did pioneering work with its partner companies and tested a method for making new glass from damaged car glass – instead of turning it into insulation material or hollow glass, as is usually the case. Audi uses this plate glass in series production of the Audi Q4 e-tron models, thus creating a cycle that is so far unique at Audi. With regard to plastics, the company is pursuing several approaches at the same time in close cooperation with scientists and research institutions: Alongside conventional, mechanical recycling, chemical and physical recycling are also being tested. It’s important to note that Audi doesn’t stop at researching. To help conserve resources, recycled plastics are already being used now for more and more parts. In the Audi Q4 e-tron you can already find up to 27 parts containing recycled materials.