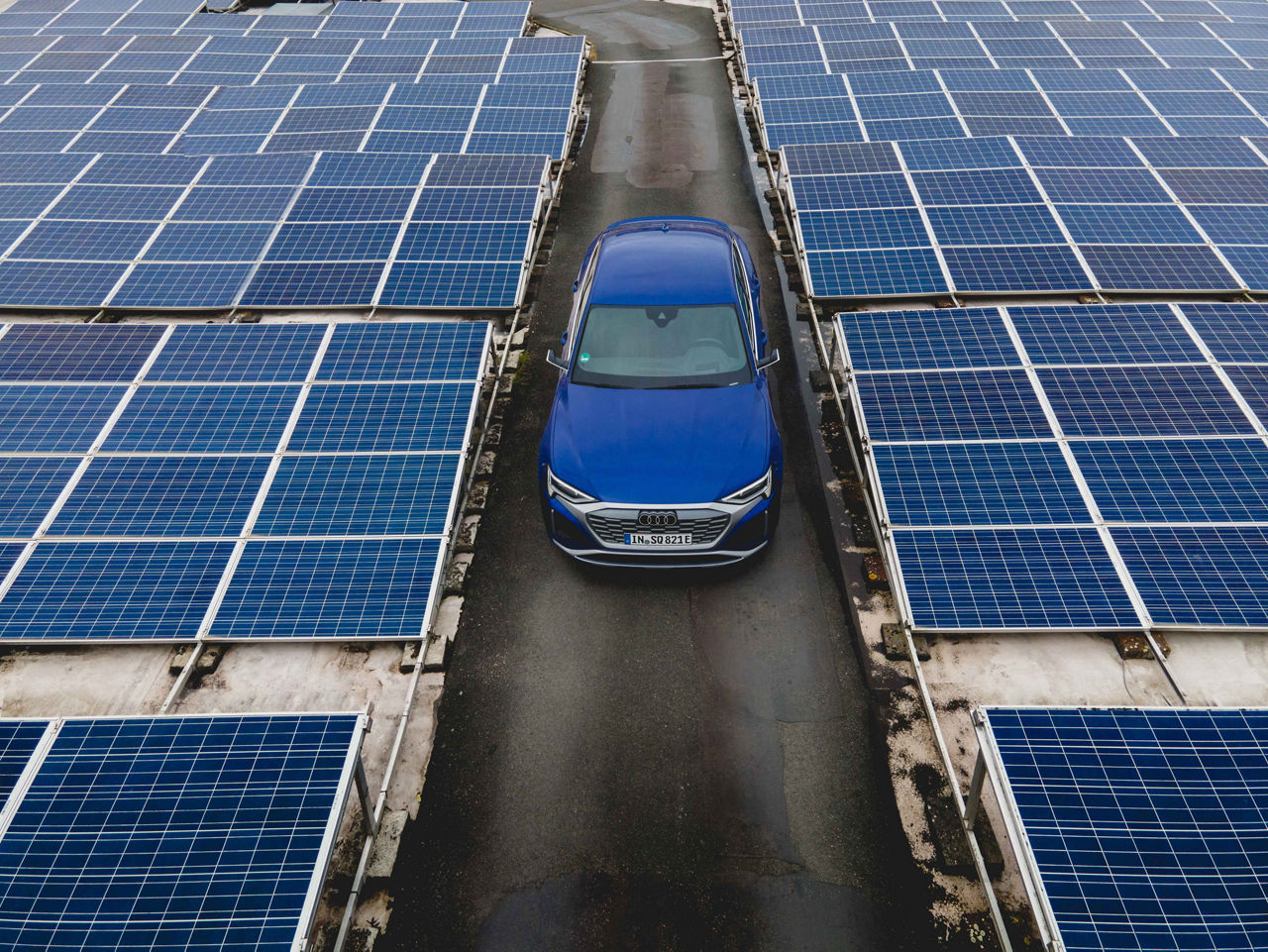
Climate change is one of the greatest challenges of the present time. Audi is conscious of the impacts of its products and business operations on the environment and society. Greenhouse gas (GHG) emissions occur at all stages of the automotive value chain and may have negative environmental impacts.
By 2050* at the latest, the Audi Group aims to achieve net carbon neutrality* across the entire value chain. Progress is measured using the decarbonization index (DKI),* with measurements performed for the individual Volkswagen Group brands and the Group as a whole.
The DCI* is a strategic indicator on the path to net carbon neutrality.* With the aid of the DKI,* Audi calculates the average emissions of CO₂ and CO₂ equivalents* over the entire life cycle of its passenger car portfolio and states them in metric tons of CO₂ per vehicle. The DCI includes both direct and indirect GHG emissions at individual production sites (Scope 1* and 2* in 2024: 0.29 million metric tons CO₂e*) as well as all other direct and indirect GHG emissions over the life cycle of the vehicles (Scope 3* in 2024: 48.6 million metric tons CO₂e*).
One approach to identifying reduction potential for the environmental impacts of vehicles is the life cycle assessment.* This examines the environmental impacts of selected vehicles throughout their entire life cycle (cradle-to-grave), with all steps along the value chain for each individual part being considered in the generic life cycle assessment. Based on this assessment, GHG reduction measures and optimization potential are identified, evaluated and implemented across the entire life cycle. Using this process, it was possible to reduce the carbon footprints of the Audi Q6 55 e-tron quattro* and Audi A6 Avant e-tron* by 35 percent, for example. A substantial contribution came from GHG-reducing measures in the production and the use of green electricity in the utilization phase.
Decarbonization of the supply chain
The proportion of GHG emissions in the supply chain is increasing due to the consistent electrification of the Audi vehicle portfolio.* To counter this increase, the Audi CO₂ program was launched in 2018. In cooperation with supplier companies, it identifies CO₂ mitigation measures and optimization potential throughout the entire production process for materials and components. So-called hotspots are used to identify specific materials or components in the company that are expected to offer the greatest savings potential. The biggest emissions driver in the supply chain for an electric vehicle is the high-voltage battery, followed by parts made of aluminum and steel. All of the components in these three areas together are generally responsible for approximately 70 percent of the carbon footprint in the supply chain of an electric vehicle.
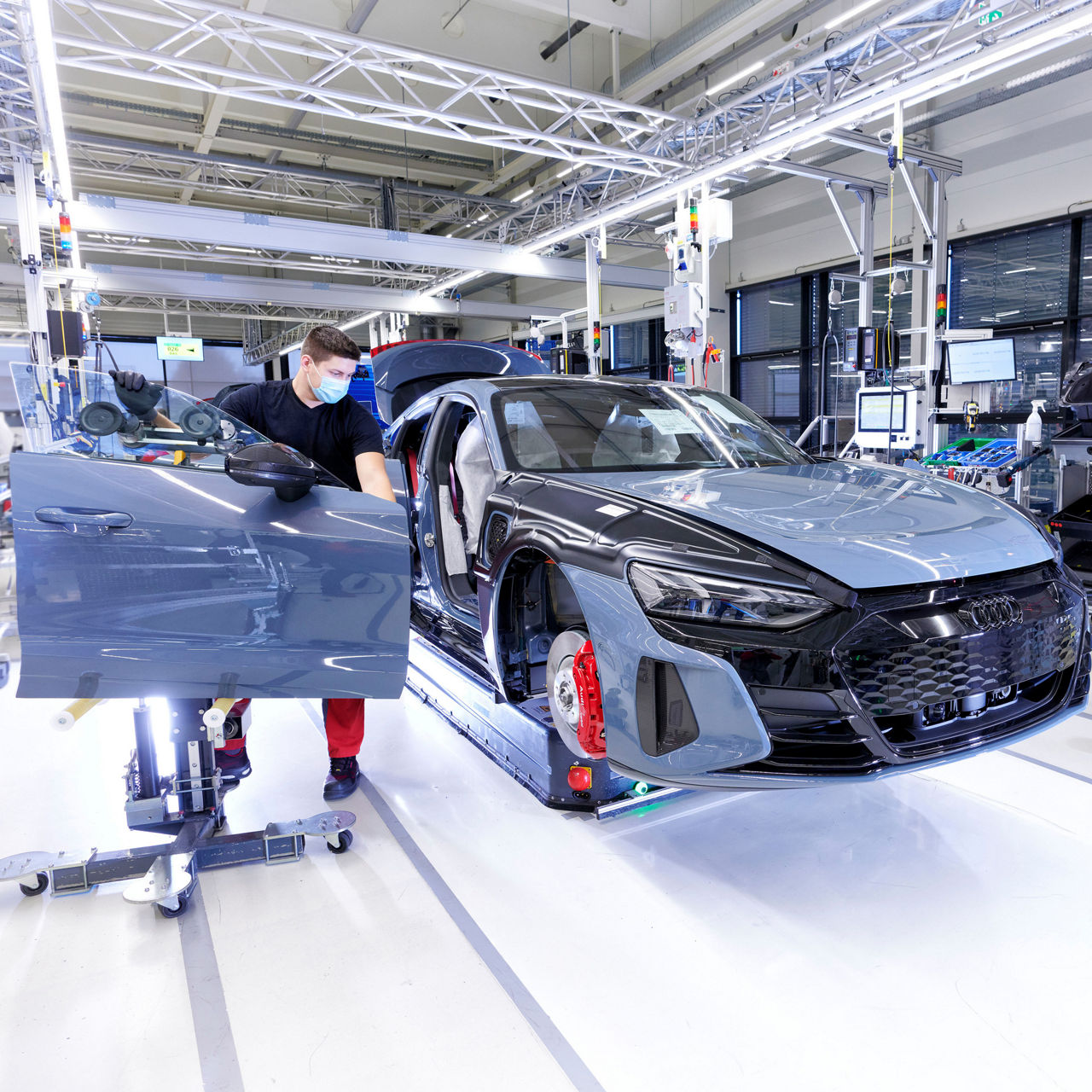
More details
In the future, Audi plans to increase the proportion of raw material loops and the use of recycled materials in vehicle projects. An example of this is the Aluminum Closed Loop, which has been implemented since 2017. Aluminum sheet offcuts that are produced in the press shop are sent straight back to the suppliers. The suppliers recycle these into aluminum sheets of equal quality, which Audi then uses again in production. Compared with production of primary aluminum, the energy requirement is reduced by up to 95 percent, with a corresponding reduction in CO₂ emissions. Like the press shops in Ingolstadt, Neckarsulm and Győr, the plant at the Münchsmünster site has been part of the Aluminium Closed Loop since 2024. In 2024 alone, the Aluminum Closed Loop process as well as other measures delivered net savings in the supply chain of approximately 350,000 metric tons of CO₂e.* These measures include the use of CO₂e*-reduced materials and the use of green electricity in the production of high-voltage battery cells.
Decarbonization of production
The Mission:Zero environmental program combines all the company’s initiatives for reducing the ecological footprint in production and logistics. There are four action areas: water usage, biodiversity, resource efficiency and decarbonization. The goal of the decarbonization action area, to achieve net carbon-neutral production* at all Audi production sites* from January 1, 2025, was reached. Since January 1, 2025, production at the plants in Neckarsulm (Germany) and San José Chiapa (Mexico) – and thus all Audi production sites* – has been net carbon-neutral.* The other sites had already achieved this goal in previous years: Ingolstadt (Germany) in 2024, Győr (Hungary) in 2020 and Brussels (Belgium) in 2018. Net carbon-neutral* production includes GHG emissions generated directly at the site (Scope 1),* and indirect GHG emissions from energy purchased through external utilities (Scope 2).* External auditing companies are called on annually to verify and certify the net carbon neutrality* of the Audi production sites.*
The net carbon neutrality* of the Audi production sites* was achieved with the following steps:
- Increase energy efficiency
- Produce own renewable energy
- Purchase renewable energy
- Offset the currently unavoidable GHG emissions through climate action projects Increase energy efficiency
In 2024, the company cut energy consumption at the production sites* by just under 73,000 megawatt hours compared with the previous year. This is equivalent to a CO₂ reduction of more then 7,700 metric tons and cost savings of around EUR 8.4 million. As a result, achievement of the energy-saving target was 108 percent in 2024. The basis for this was over 470 implemented efficiency measures from the Mission:Zero program.
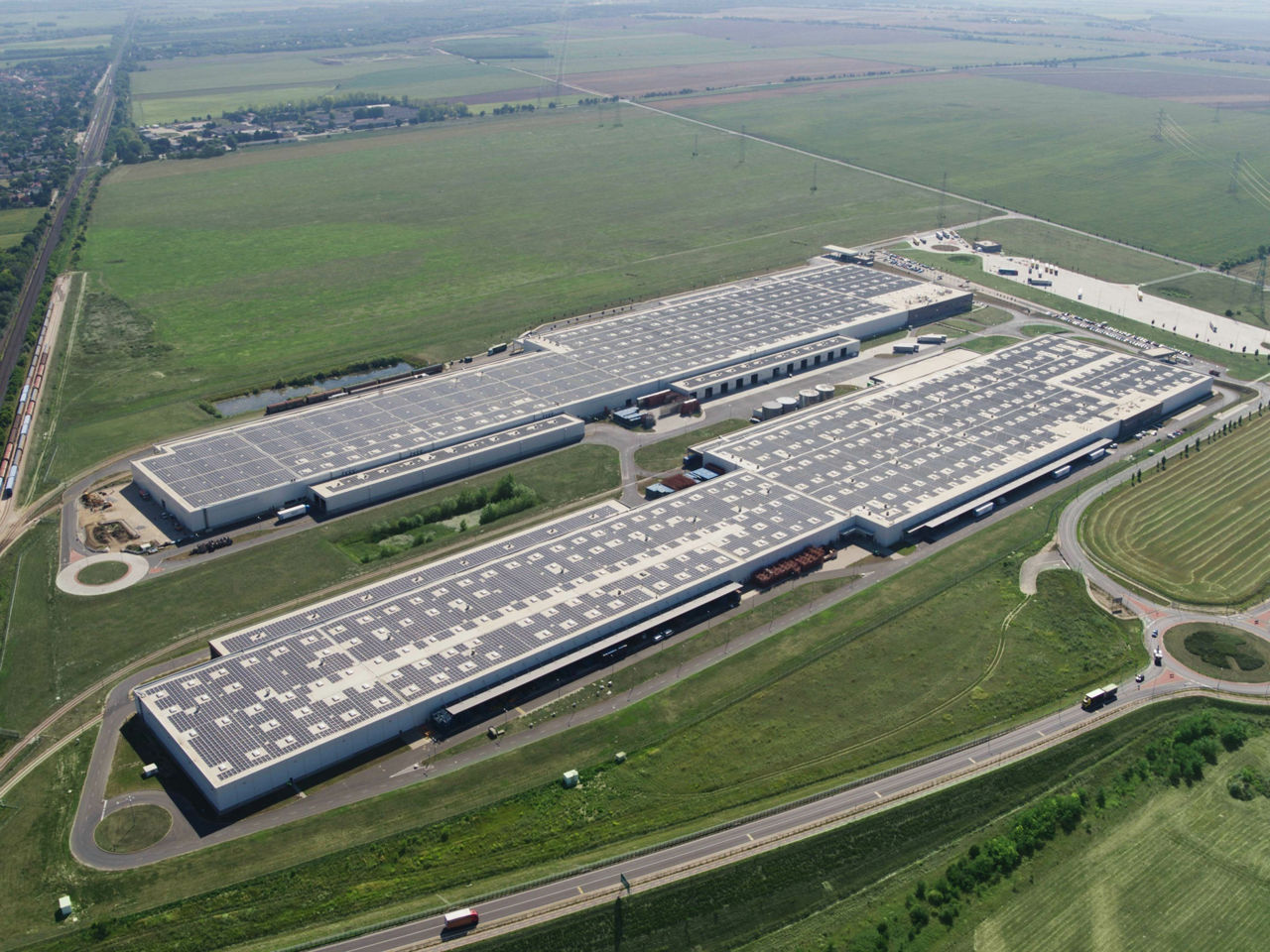
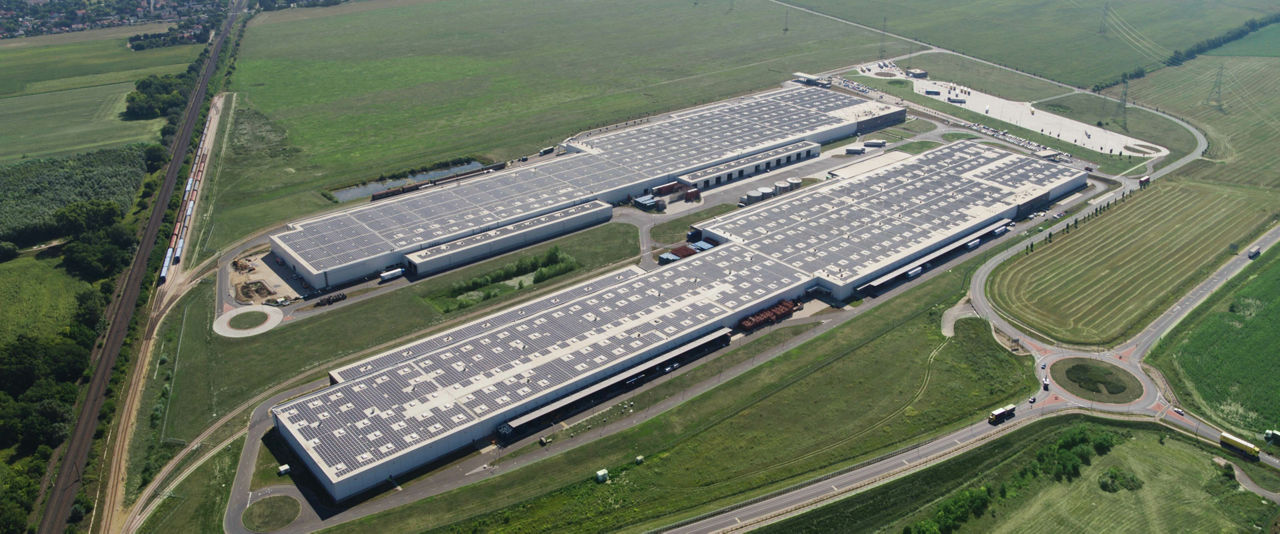
Audi Hungaria: photovoltaic system on the roofs of the two logistics halls.
Audi Hungaria: photovoltaic system on the roofs of the two logistics halls.
Produce own renewable energy
At the following production sites,* Audi expanded capacities to produce its own renewable energy:
Purchase renewable energy
When purchasing energy, Audi ensures that it comes from renewable sources. Since 2021, all Audi production sites* have used electricity from renewable energy sources only. The Ingolstadt production site, for example, switched to green electricity back in 2012.
Offset the currently unavoidable emissions through climate action projects
Despite the large number of measures implemented, GHG emissions remain that have been unavoidable until now due to technical, process-related or economic limitations. This is the case, for example, for the operation of test rigs on which diesel and gasoline engines are tested. The company offsets these GHG emissions by purchasing offset certificates for GHG emissions from external climate action projects, which have to fulfill strict quality standards.
Decarbonization of logistics
Measures to reduce GHG emissions in logistics are likewise part of the Audi Mission:Zero environmental program. In collaboration with Volkswagen Group Logistics, the company is following a long-term roadmap to organize transport to and from the plant in such a way that as little CO₂ as possible is emitted.
The following measures contribute to achieving this goal: By using smart control methods to consolidate shipments, Audi is able to avoid transport operations. In addition, capacity utilization and routes are optimized continuously to reduce transport operations and CO₂ emissions. As a way of achieving further savings, Audi uses more climate-friendly forms of transport such as rail. The combination of different forms of transport, such as rail and road, allows the most varied logistics requirements to be addressed flexibly and more efficiently. In April 2024, Audi commenced operation of its first block train between Regensburg and Lébény (Hungary) in combination with upstream and downstream transportation by truck. This train links the Ingolstadt and Neckarsulm plants as well as the vehicle and engine plant in Győr. Thanks to the use of innovative wagon handling technology, the block train can be operated independently of the equipment that is usually necessary at the terminals. This has reduced truck transportation by around 185,000 kilometers per week, which will make it possible to reduce CO₂ emissions by up to 11,500 metric tons per year in the future.
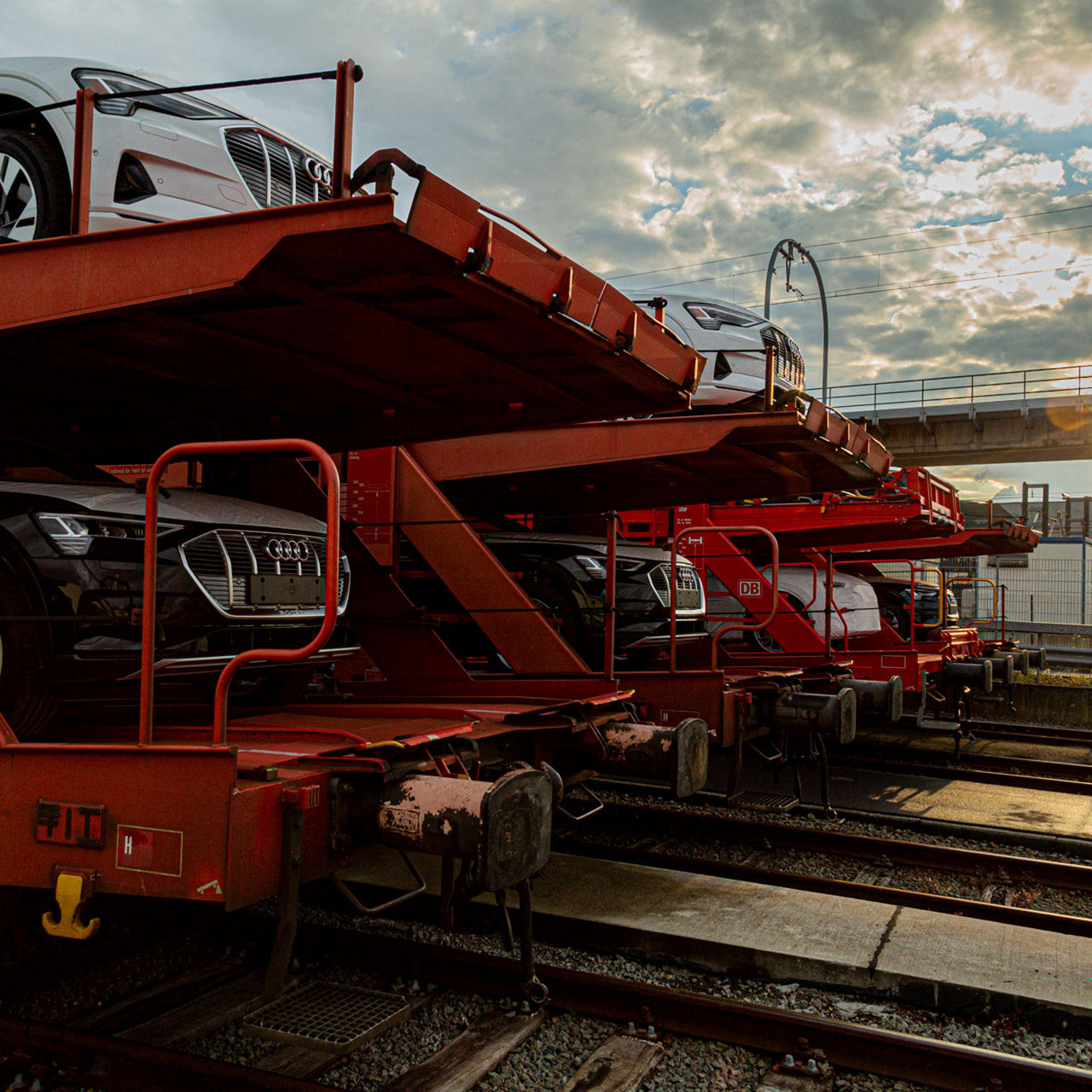
In close collaboration with truck manufacturing companies, fuel producers and forwarding agents, Audi is deliberately focusing on biogenic fuels, such as bio-LNG and HVO100, as important bridging technology. These fuels generate up to 85 percent fewer CO₂ emissions compared with the use of diesel in road transport. Truck transportation in Germany upstream and downstream of the block train has already been switched to the use of HVO100 biogenic fuel. In addition, use of Battery Electric Trucks (BET) is being piloted in inbound logistics (procurement and production logistics). At the start of 2025, BETs were introduced on two test routes and cover a total distance of some 120,000 kilometers each year. The goal is to prepare for the deployment of BETs in series production at other Audi locations.
Overseas transport represents the largest single lever for decarbonizing finished vehicle logistics. Step by step, Audi is increasingly focusing here on alternative drive systems such as ships that run on LNG (liquefied natural gas).
Decarbonization in the utilization phase
A significant proportion of GHG emissions that a vehicle emits over its life is generated at the utilization phase, in other words by actually driving the vehicle. Electric cars are operated without causing any local GHG emissions and can therefore contribute significantly to reducing GHG emissions. And if they are also charged with green electricity, this improves the carbon footprint over the entire life cycle of the vehicle. Audi is successively expanding its e-portfolio, The company currently has 10 BEVs in its portfolio, six of which were presented in the 2024. The last major world premieres of new model series with internal combustion engines will take place in 2026. In addition, fully electric vehicles will become more efficient. For example, vehicles based on the new Premium Platform Electric (PPE) are up to 30 percent more efficient in terms of energy consumption than the Audi e-tron* (first generation). This is due to the use of cutting-edge technologies and systematic optimization of the entire system, consisting of electric motor, transmission and power electronics as well as improved aerodynamics. Compared with the electric drive systems that have been developed and installed to date, all the PPE drive components are more compact and more efficient. The PPE electric motors need around 30 percent less space and their weight is some 20 percent lower than the powertrains in existing electric models. With high-performance, compact and highly efficient electric motors, a newly developed lithium-ion battery consisting of 12 modules and 180 prismatic cells with a total gross capacity of 100 kilowatt hours (94.9 net kilowatt hours), the Audi Q6 e-tron,* for example, is the first PPE series-production model with a range of up to 625 kilometers according to WLTP. With a drag coefficient of 0.21, the Audi A6 Sportback e-tron* is the most aerodynamic Audi vehicle ever and in this regard also tops its segment within the Volkswagen Group as a whole.
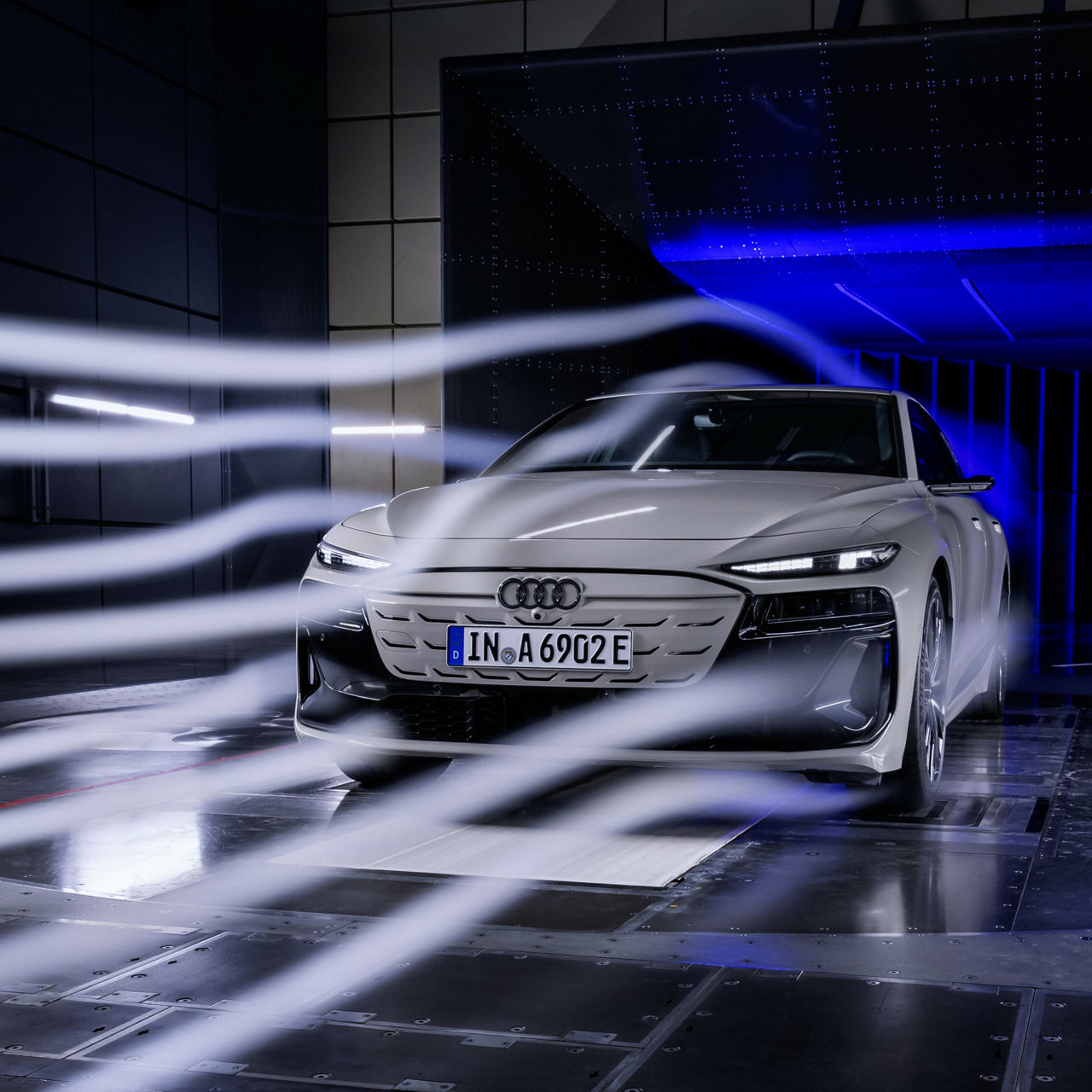
With a drag coefficient of 0.21, the Audi A6 Sportback e-tron* is writing Audi history.
More details
At Audi, one key lever for reducing CO₂ emissions is the electricity used to charge the company’s electric fleet. Even today, for example, Audi customers can use green electricity offered by the Volkswagen subsidiary Elli (Electric Life) for charging at home. Meanwhile, the charging network operated by Ionity supplies green electricity for charging on the road. The joint venture, of which the Volkswagen Group is a member with the Porsche and Audi brands, operates more than 4,500 charging points in 24 European countries, making it the largest pan-European high-power charging network with a charging capacity of more than 250 kW that is available for all electric vehicle brands. In addition, Audi offers customers a service for charging at public charging terminals with Audi charging.* Audi drivers therefore have access to around 700,000 charging points in 29 countries in Europe. The Audi network of fast-charging stations, or Audi charging hubs as they are known, was expanded in 2024. In addition to the charging points in Berlin, Munich, Nuremberg, Salzburg and Zurich, others in Bremen, Frankfurt and Tokyo came into operation during the reporting period. A second Audi charging hub in Tokyo and others in Germany are already planned.
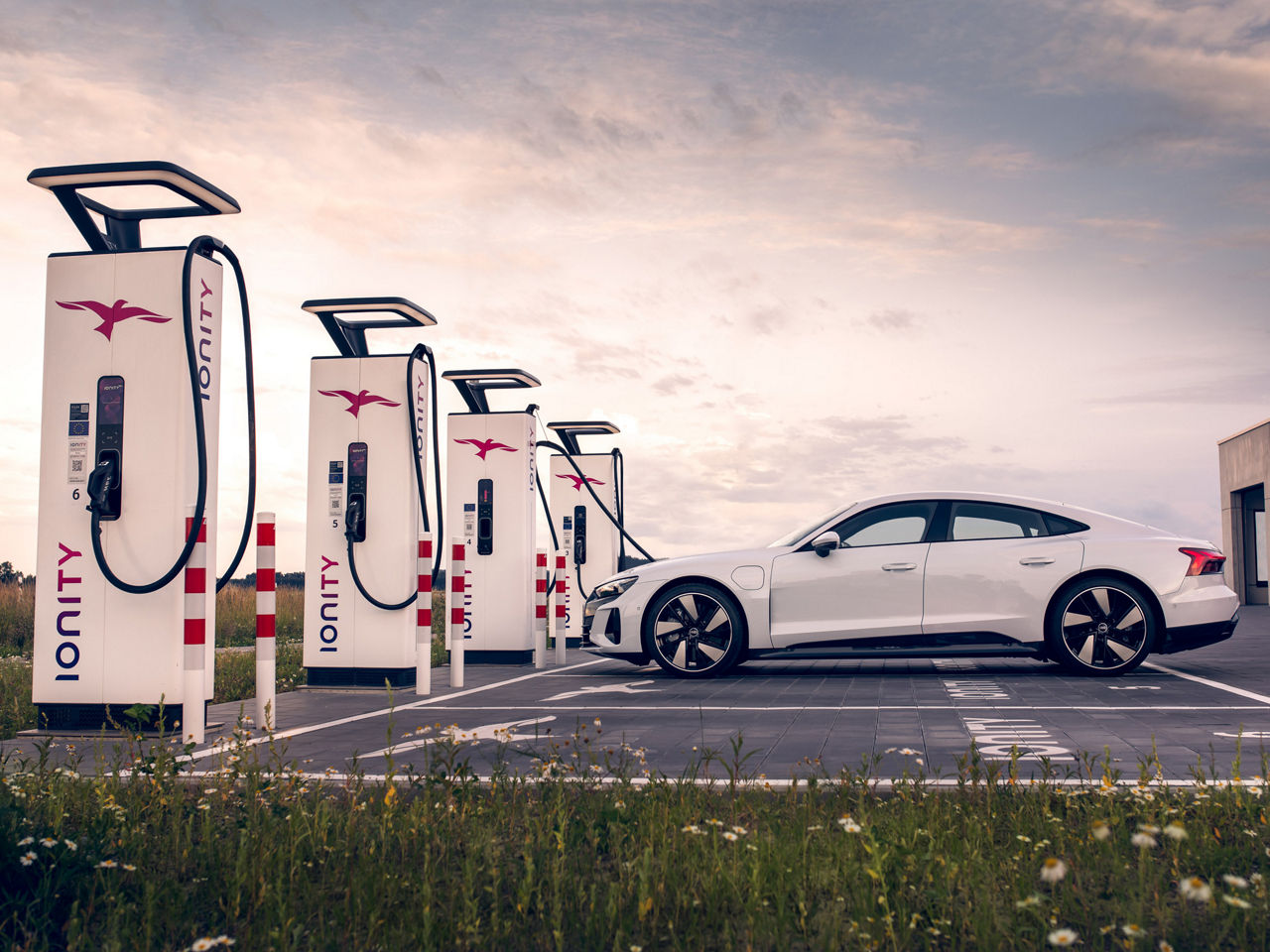
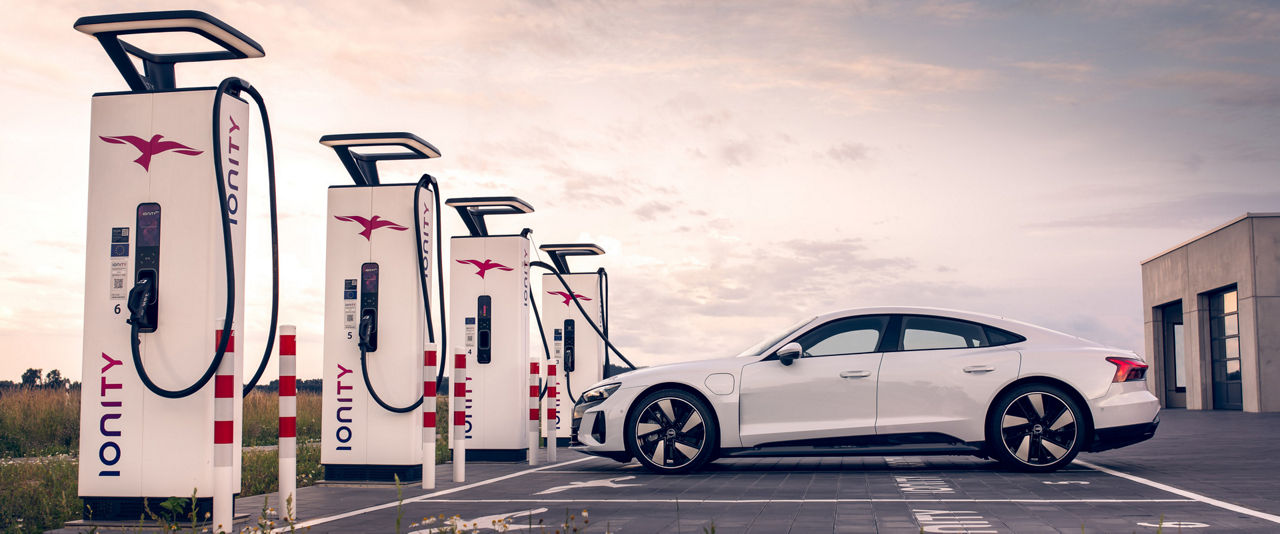
Audi is supporting the expansion of renewable energies. In cooperation with VW Kraftwerk GmbH, Audi is co-funding various projects aimed at developing renewable energy such as photovoltaics or wind power – all told some 26 green electricity projects in nine European countries. Since this voluntary initiative was launched in 2021, these green electricity projects have fed around 1.8 terawatt hours into the European electricity grid. VW Kraftwerk GmbH is driving the expansion of renewable energy across Europe. Support is currently being provided for 18 photovoltaic facilities and eight wind farms in Finland, Germany, Italy, the Netherlands, Poland, Portugal, Spain, Sweden and the United Kingdom. This support is intended to be long term, usually lasting 10 years. The projects contracted up to and including 2024 now continuously produce around one terawatt hour of green electricity annually.
Audi is also pushing for a reduction in CO₂ emissions in retail together with the Volkswagen Group. The Volkswagen Group dealership network for all brands is present in more than 150 markets worldwide with over 17,000 dealer and service locations that generate a corresponding amount of CO₂ emissions. For this reason, a number of Volkswagen Group brands initiated the „goTOzero RETAIL“ project in 2021. The vision is a dealer and service network with a minimum of negative environmental impacts. To this end, the Volkswagen Group has set its global dealer and service network ambitious targets for reducing its carbon footprint. Starting from the first measurement in 2020, which gave a baseline value of 3.22 metric tons of CO₂ emissions, the aim is to reduce the carbon footprint by at least 30 percent by 2030, at least 55 percent by 2040 and, lastly, at least 75 percent by 2050. Unavoidable CO₂ emissions will be offset. Training courses and manuals are made available to the businesses to help them identify and successfully implement essential decarbonization measures. In addition, an assessment system was developed called “goTOzero RETAIL certification.” It is based on the ISO 14001 standard and on requirements of certification institutes for buildings and ESG rating agencies such as MSCI, ISS and Sustainalytics. The goTOzero RETAIL certification has now been rolled out in 18 markets worldwide and has been performed successfully at 67 dealers. A total of four levels (bronze, silver, gold and platinum) are possible and reflect the level of compliance with the underlying list of requirements. The first platinum certificate was awarded to a dealer in France.
Whereas the “goTOzero RETAIL” initiative has the goal of supporting the global dealer and service locations on their path to reducing CO₂ emissions, the Audi-specific “e-Readiness check” is a comprehensive assessment of the current status of the charging infrastructure offered by a dealer or service partner. Each participating dealership is provided with an individual implementation plan to help achieve its goals, such as improving charging capacity. It was introduced in 2023 and has been implemented successfully in 13 markets and more than 650 dealerships across Europe. Other markets in Europe as well as in Central America and the Middle East will follow in the course of 2025.
Decarbonization in the end of life: circular economy and second life
AUDI AG is also optimizing the last phase of the life cycle of a vehicle by returning some materials to the value chain following the utilization phase of the vehicles. This should allow key resource cycles to be closed gradually. In terms of electric cars, the lithium-ion battery is one part that is of particular importance with regard to recycling. High-voltage batteries can continue to be used meaningfully even after many years of service on the road. Audi is pursuing three possible reuse objectives in cooperation with the Volkswagen Group: firstly remanufacturing, which involves using recycled high-voltage batteries again in electric vehicles. The second involves so-called second-life concepts, which give batteries a second life for years outside of an electric vehicle – for instance in the fast-charging stations of an Audi charging hub. And the third is efficient recycling. This is done in Germany, for example, at a Volkswagen pilot plant in Salzgitter.