Not a matter of location: sustainability at Audi
Audi plans to continue working on the gradual implementation of the most extensive possible circular economy and sustainable production by 2030.
missing translation: fa.article-intro.reading-time – 08/23/2023
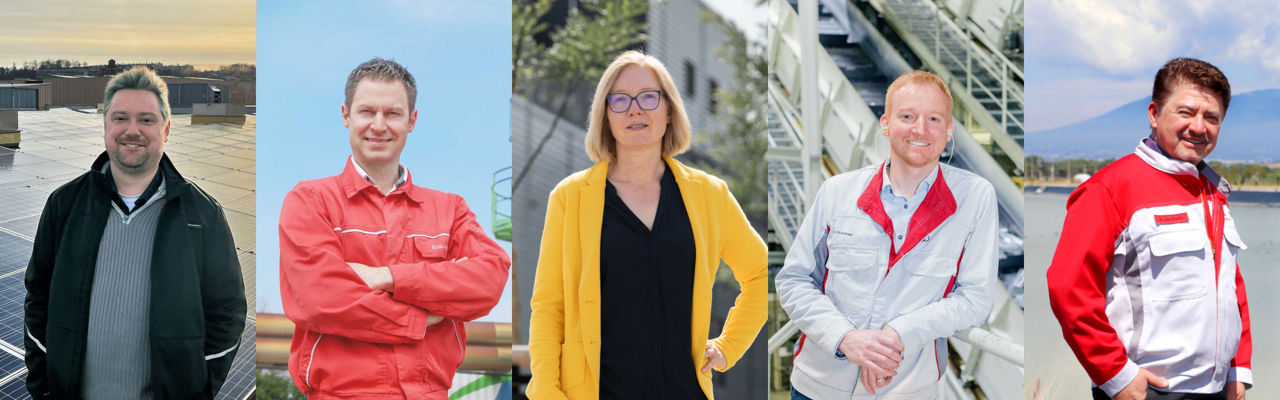
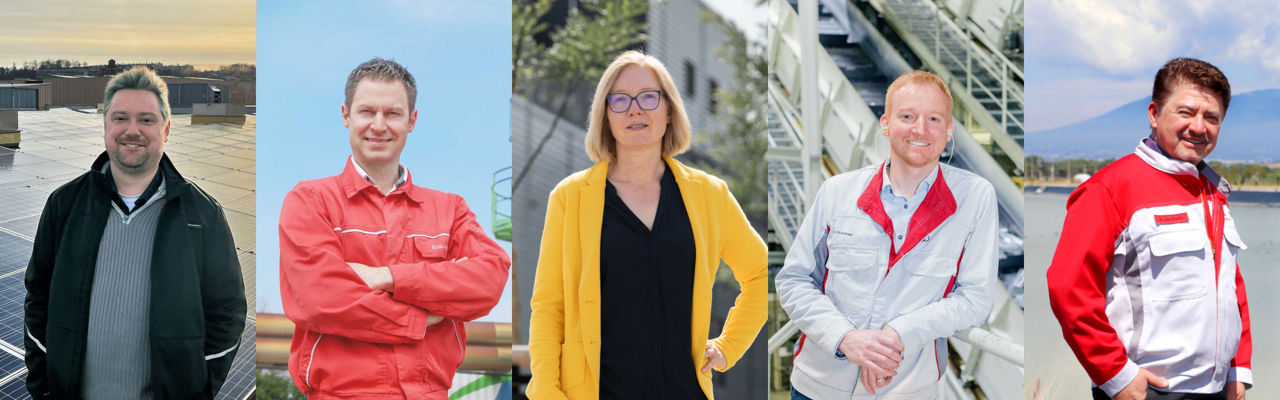
By 2025, Audi sites should be as CO₂-neutral* as possible in terms of their balance sheets. This means that further adjustments will also be made in the supply chain and at production sites. We visited five sites and spoke with those responsible about their ongoing projects.
Our first stop: Audi Brussels. The site is a benchmark for sustainable production at Audi. Since 2018, the plant has been operating on a CO₂-neutral* balance sheet and is thus leading the way for Audi’s strategic environmental program Mission:Zero. The success of the site in Belgium is based on several initiatives that cleverly interlock and complement each other to form a future-oriented overall package. One element is the use of electricity from photovoltaic systems to the largest possible extent. More than ten years ago, the site installed one of the largest photovoltaic systems in the region. Today, the plant produces around 15 percent of its own electricity consumption.
Progress in decarbonization is also a priority in transportation. The electric drives from Hungary arrive in Brussels mainly by freight trains. Freight transport has been running on the approximately 1,300-kilometer route between the two sites since May 2022. “In recent months, we have shifted the normal transport of components from road to rail,” says environmental coordinator Christian Stragier.
“This switch saves around 3,800 tons of carbon dioxide per year.” And he is definitely not ready to sit back and relax. “We have by no means exhausted our on-site potential (of the site). In future, we want to generate up to 25 percent of the electricity (for production) ourselves,” explains the environmental expert.
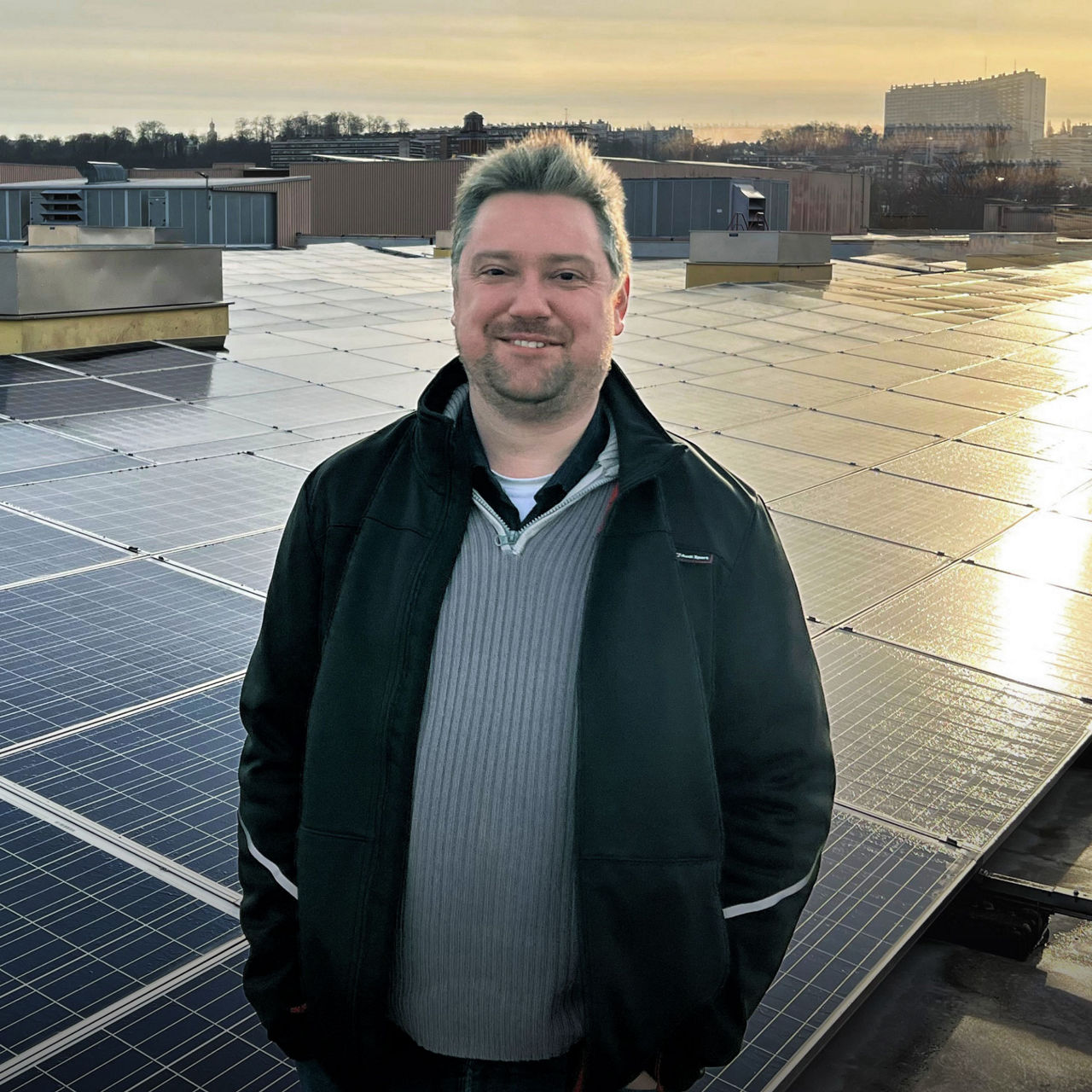
Christian Stragier, Environmental Officer at Audi Brussels
Rainwater: from the lagoon to production
Clean drinking water is one of the world’s most valuable resources and is the fundamental basis of all ecosystems. Smart water management that takes nature’s concerns into account is therefore also at the heart of Audi’s sustainability efforts at its plant in San José Chiapa, Mexico.
A gigantic lagoon shimmers on the factory site at an altitude of 2,400 meters. The lake – a man-made water reservoir with a capacity of 234,000 cubic meters – fills up depending on the amount of water during the approximately six-month rainy season from April to September. The collected and treated rainwater can be used in various processes and reduce water stress.
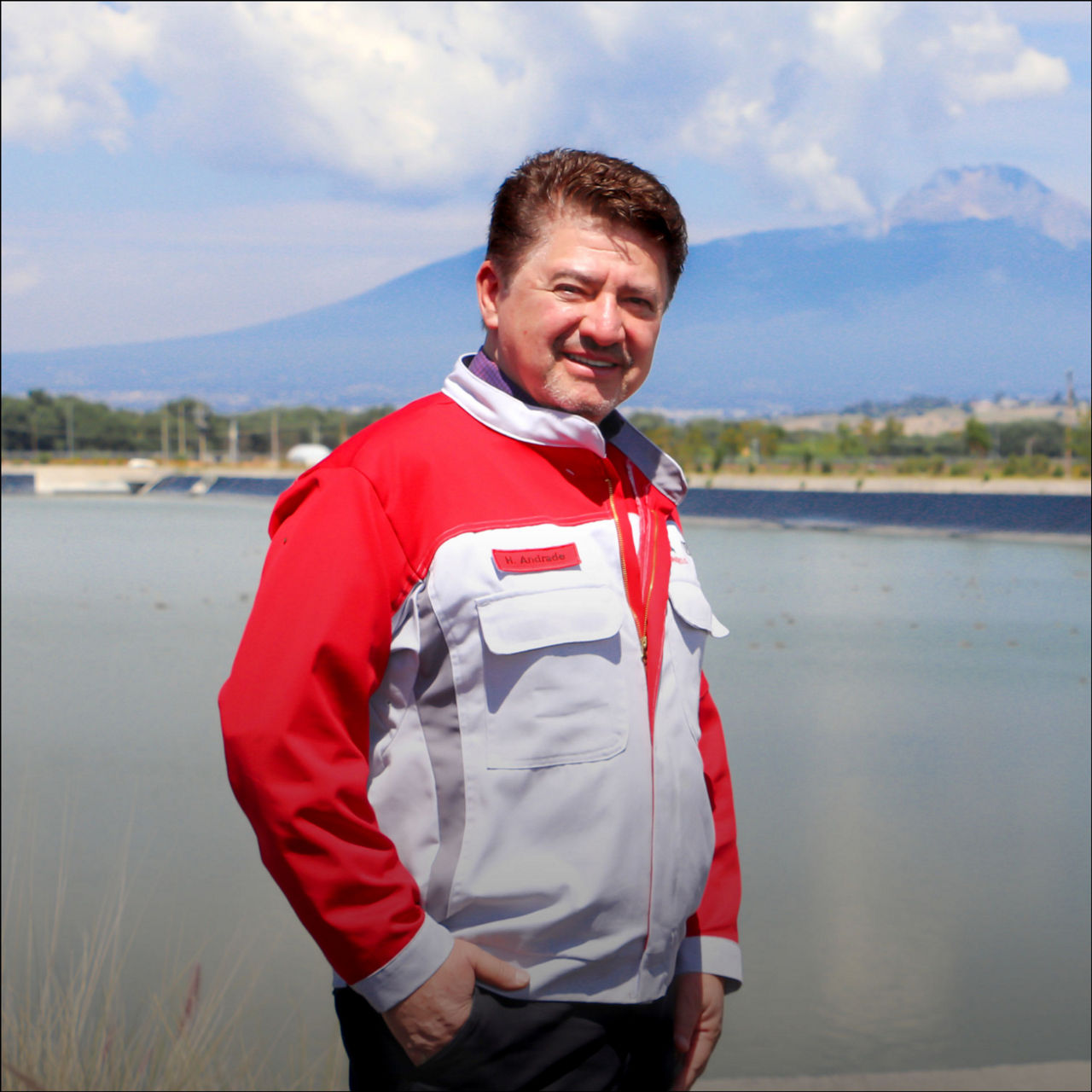
Héctor Andrade, Head of Environmental Protection at Audi Mexico
“We built this lagoon in 2014, even before we started production here,” says Héctor Andrade, head of environmental protection at the San José Chiapa plant since 2022. “I firmly believe that dealing with the growing scarcity of water is an imperative task that must be addressed worldwide.”
In San José Chiapa, the water cycle is almost completely closed. “A few years ago, we built a reverse osmosis plant with which we recycle our water so that it can be reused in the production processes. This has allowed us to significantly reduce the amount of water the site needs,” explains Andrade.
“
The Neckarsulm site proves that recycling can be cleverly integrated into production.”
Heiko Wimmer
In the cycle: recycling aluminum
In addition to reduced raw material consumption and the reuse of water, recycling is one of the fundamental elements of sustainability. The Neckarsulm site proves that recycling can be cleverly integrated into production. Here, aluminum scrap is collected and taken for processing.
Only unmixed aluminum can be reprocessed without any loss of quality. As head of maintenance at the press shop, Heiko Wimmer therefore ensures the cleanliness of the raw material. A magnetic separator removes magnetic metals from the aluminum. Foreign substances such as iron could cause “the melt to tip” in the recycling process, explains Wimmer. The Audi plant in Neckarsulm currently recycles around 11,500 tons of the raw material per year.
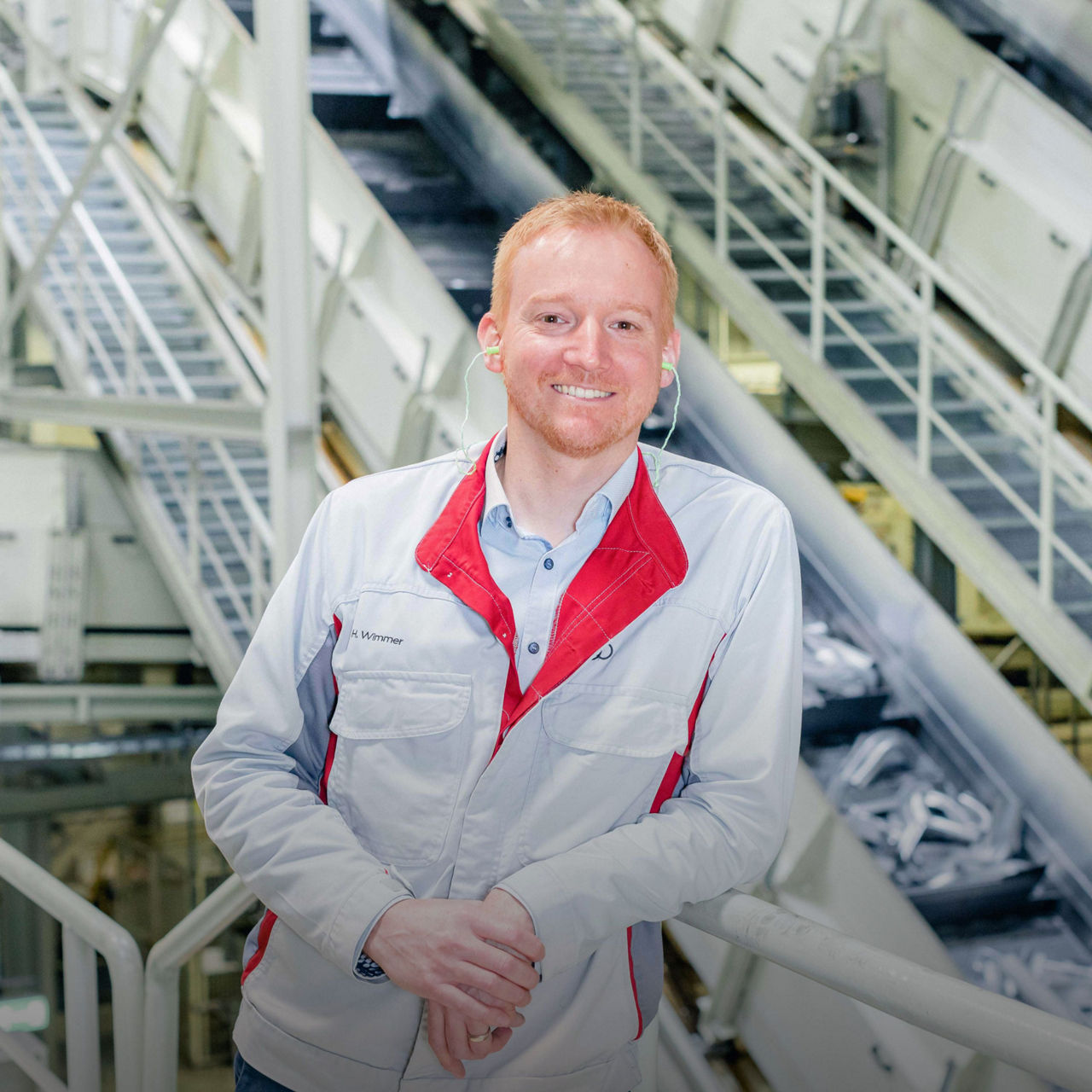
Heiko WImmer, Head of Maintenance Pressing Plant Audi Neckarsulm
Geothermal and solar energy
The Audi plant at the Győr site demonstrates what a versatile sustainability concept can look like. 12,000 employees produce 1.6 million engines here every year. Making an output like this as sustainable as possible is no mean feat. Peter Elias, Head of Environmental Management in Győr, explains: “Four focal topics determine our measures: balance sheet CO2 neutrality*, reduction of water consumption, resource-efficient recycling management and preservation of biodiversity.”
The first steps have been taken. This is evident, for example, in the 160,000 square meter photovoltaic system on the roofs of the two logistics centers. There is also the geothermal plant, which not only covers 70 percent of the plant’s heating requirements, but also supplies district heating to the nearby city of Győr. In addition, aluminum is recycled at Audi Hungaria – like in the process in Neckarsulm and Ingolstadt – and returned to production.
Further measures are being planned: For example, photovoltaic capacity is to be further expanded in 2024. “In addition, demand-driven production steering holds great potential for further reducing energy consumption,” explains Elias. The careful use of water is the next major goal: “Reducing water consumption will become just as important as saving CO2.”
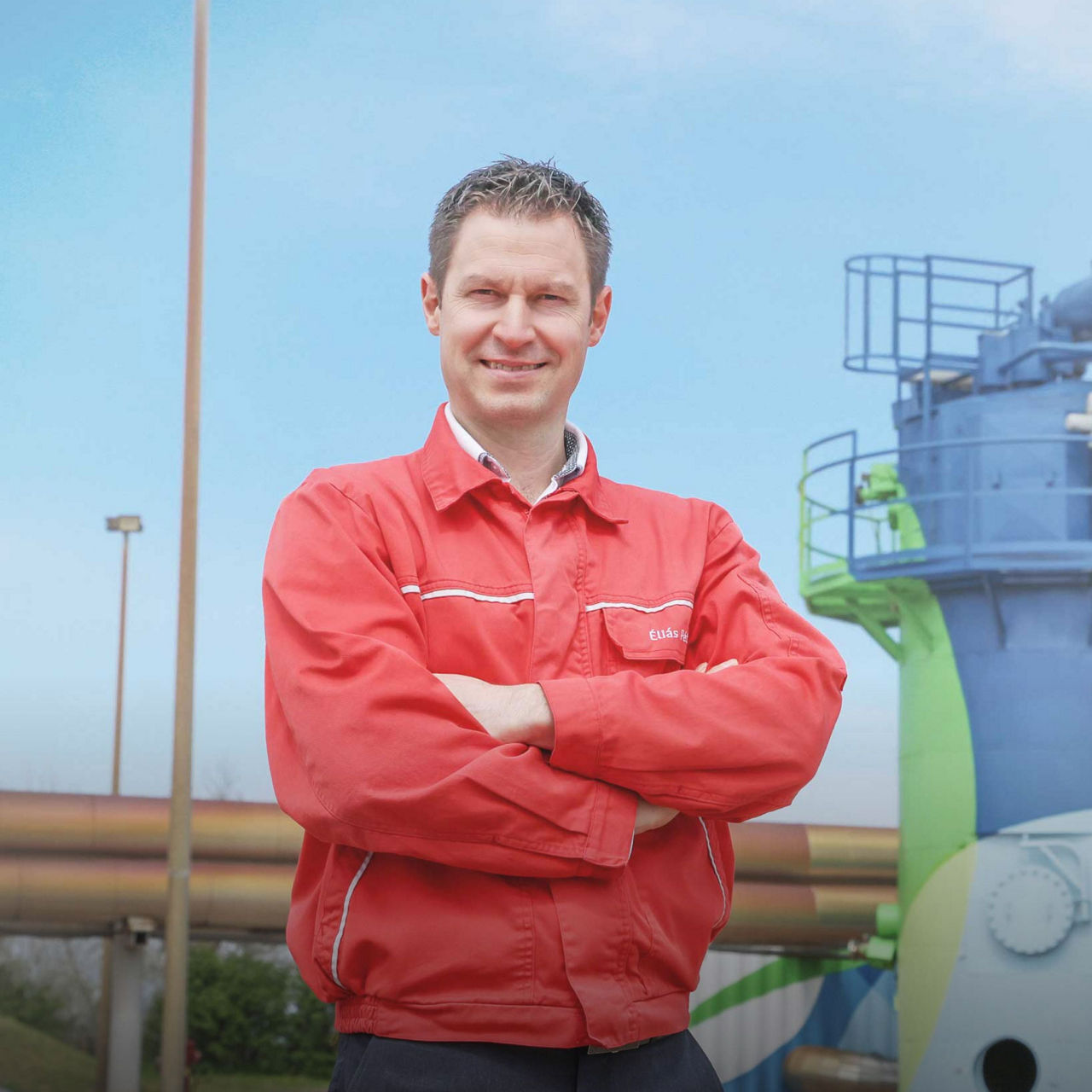
Peter Elias, Head of Environmental Protection at Audi Hungaria
From industrial wasteland to technology park
The incampus technology park in Ingolstadt clearly shows that a determined commitment to the environment pays off. Where IT experts and others are today developing solutions for the future, various petroleum products were being produced until 2008 – with consequences for the soil. At that time, 1,200 exploratory drillings and 50,000 laboratory analyses of the samples revealed a complicated situation: 22 hectares of land were contaminated and in need of remediation. The soil contained 900 tons of heavy oil, 200 tons of light gasoline, and toxic chemicals from the extinguishing foam of the former company fire department.
The site, in a beautiful location between Ingolstadt’s old town and the Danube, is a real gem. “The site is optimally located with direct access to the A9 highway. With its sustainable concept, incampus creates ideal conditions for innovative and globally networked business,” says Marlen Riddering, Environmental Officer for AUDI AG’s Bavarian sites. After years of extensive remediation, the ground is now free of pollutants to such an extent that it can be used again. Today, catering facilities and freshly planted trees invite visitors to linger. “Together with our partners, we have created a site here that is truly valuable,” says Riddering. The incampus technology park is one of the most modern innovation quarters in Bavaria. With its office and workshop space, smart energy center, vehicle safety center and data center as a digital nerve node, it proves how sustainable concepts and clever innovations can be seamlessly brought together.
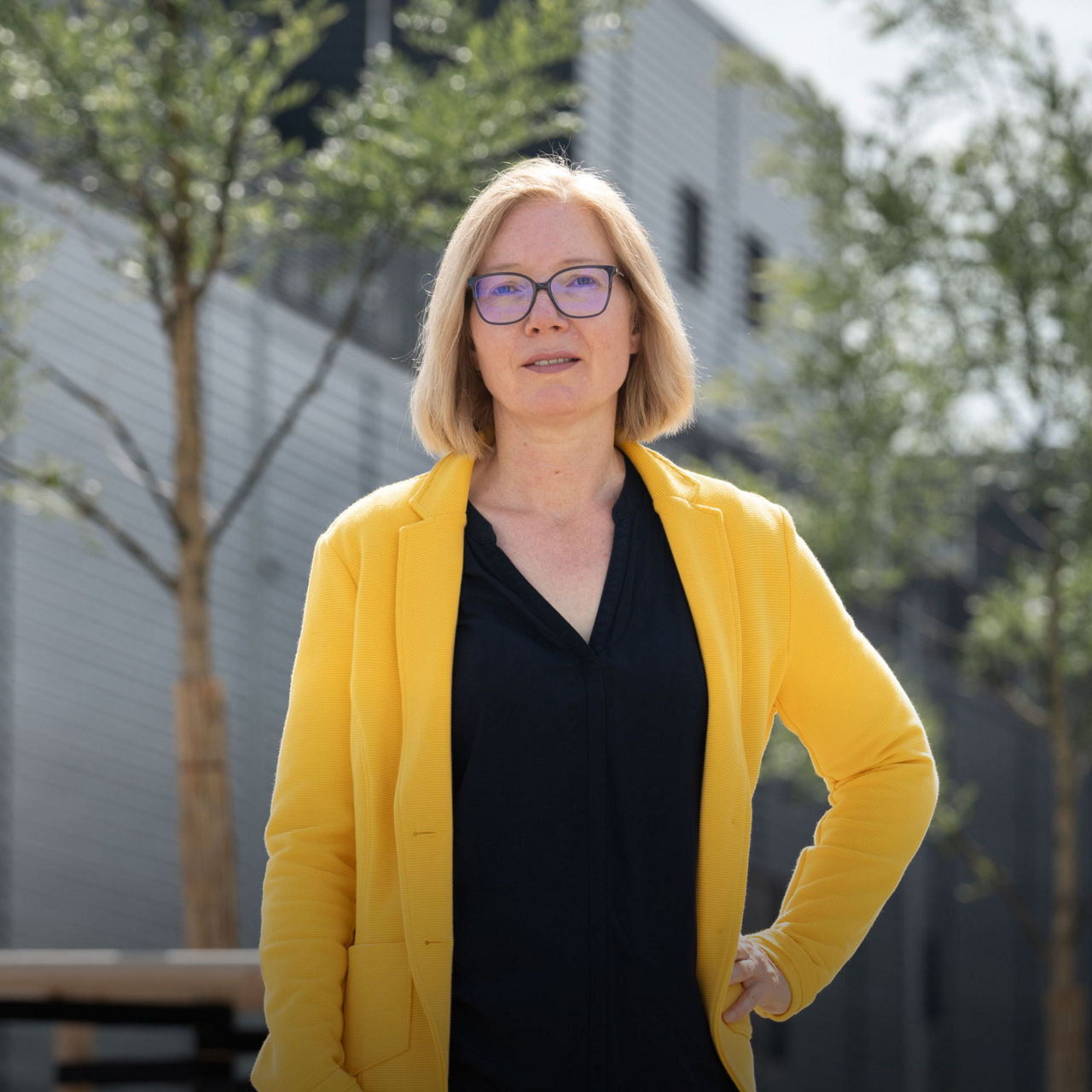
Marlen Riddering, Head of Environmental Protection at Audi Ingolstadt